Woven Fabrics
Tantra Composite Technologies offers wide range of woven fabric constructions include plain, twill and satin and their derivatives weave patterns also more complex designs for visual and performance applications. Through internal fabric design experts, custom fibre selections put into appropriate weave patterns, fabrics can be tailored to suit each individual application.
Merits:
- High quality and zero defect fabric
- Expert fabric design team
- Widths from 0.5m – 1.5m
- Tantra Composite processes fibres from 1K to 24K, covering both high strength and high modulus fibres.
3D Woven Fabrics
3D fabrics are the focus of rapid development due to their versatile physical, structural attributes and application scopes. These fabrics can be produced in various architectures which offers a great deal of opportunity to modify the weight, aesthetics, properties and cost of the various products. There are various manufacturing processes for the interlacement of yarns to produce three-dimensional (3D) fabric structures as preforms for textile composites. The manufacturing route is determined by the end-use of composites and therefore the composite industry does not solely rely on one method but a selection of methods for fabric formation.
3D Weaving technology has capabilities to produce near-net-shape structures. These near-net shaped preforms can be further processed using low cost liquid composite moulding [LCM] techniques to some extent resin transfer moulding, to produce composite components.
M/s. Tantra Composite Technologies offers a full in-house design development from original concept drawings, through to prototyping and further into series production.
Merits
- Fabric design can be optimised to improve component performance
- Through-the-thickness reinforcement significantly lowers delamination
- Mechanical performance can be enhanced through optimised fibre orientation
- 3D fabrics offer excellent permeability characteristics, thus reduced processing time.
- Production of multi-layer fabrics can be achieved through 3D weaving process
- Variety of hybrid fabrics can be produced to optimised component performance
- Complex shapes can be produced economically
Types of 3D Fabrics
- 3D Non-woven
- 3D Stitched/Tufted
- 3D Solid woven Fabrics
- 3D Hollow Fabrics
- 3D Shell
- 3D Nodal
- 3D Non-woven
- Needle Punched [Flax/PP/PLA, Sisal/PP/PLA, Banana/PP/PLA]
- Multiple layers of 2D nonwoven webs are stacked and interlocked together in thickness direction to obtain 3D nonwoven fabric. Interlocking provides through-the-thickness reinforcement in an effort to impart out-of-plane structural integrity and reduce delamination failures, Interlocking of fibres can be done by various means however, needle punching method is very common and cost effective.
2. 3D Stitched/Tufted
- Multiple layers of 2D woven fabric sheets are stacked and stitched together in thickness direction to obtain 3D stitched woven fabric. Stitching yarn provides through-the-thickness reinforcement in an effort to impart out-of-plane structural integrity and reduce delamination failures.
3. 3D Solid Woven Fabrics
Three dimensional solid woven fabric manufacturing process incorporates and manipulates yarns in the length, width, and through-the-thickness directions. The employment of the through-the-thickness yarn within the architecture differs greatly, depending on the end application of the preform. The through-the-thickness yarn is incorporated at varying levels and angles within orthogonal, angle-interlock, and multi-layer woven architectures to obtain the desired mechanical properties, such as resistance against delamination and impact damage.
- Multilayer Fabrics
- The distinctive feature of the multi-layer fabrics is that they have clearly defined fabric layers in the thickness of the fabric. Each layer is composed of a set of warp ends and a set of weft yarns. The layers are connected by weaving either the existing yarns (self-stitching) or external sets of yarns (central stitching).
- The multi-layer structure, the through-the-thickness yarns are able to be stitched with any other layers, leaving much room for structural manipulation.
- Because of the structural characteristics, multi-layer fabrics have higher yarn crimp than other 3-D fabric counterparts, which leads to low initial modulus under tensile loading along the warp and weft directions
2. Orthogonal Fabrics
- Orthogonal woven structure is a 3-D structure containing straight yarns in the three principal directions, providing a stiffer and stronger preform against tensile loading. The thickness of the orthogonal structure is indicated by the number of layers of the warp or weft yarn; there is one more layer of weft yarn than of the warp yarn.
- Yarns are basically running straight in the warp, weft, and the through-the-thickness directions. The through-the-thickness yarns travel vertically between any two weft yarn layers.
- There are two ways an orthogonal structure can be bound together i.e. orthogonal structures that use one set of through-the-thickness warp to bind the structures together are called the ordinary orthogonal structures, and those that use two sets of opposite-travelling binding warp yarns are known as the enhanced orthogonal structures
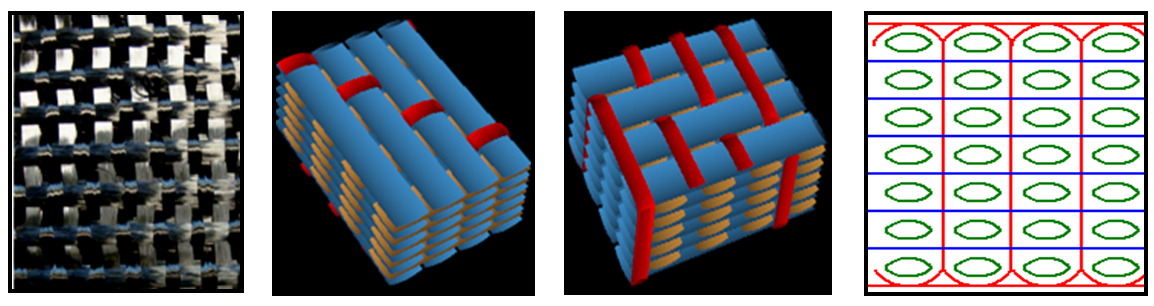
3. Angle Interlock Fabrics
- Angle-interlock structures contain a set of straight weft yarns and a set of warp yarns that weave with the weft in a diagonal direction in the thickness. In most cases, the warp yarns bind diagonally from top to bottom, and it is possible not to bind the layers of weft yarns for the full depth.
- The angle interlock fabrics have low shear rigidity, warp yarns contact the weft yarns only at the top and bottom layers; hence, the frictional resistance offered to shearing the angle-interlock fabric is lower compared to other forms of 3-D woven fabrics that use the same amount of materials.
- Low shear rigidity has led to good mouldability of the angle-interlock fabrics, and applications of such fabrics have been found in making helmet shells and in female body armour.
- Incorporation of wadding warp yarns in the structure, the tensile modulus and strength in the warp direction are sharply increased.
- Changes in the interlocking depth in this type of fabric lead to production of tapered preforms.
- There are two types of this fabric structure such as layer-to-layer and through-the-thickness
- In through-the-thickness fabric, bias yarns take a straight path along the fabric thickness until reaching to the top or bottom surface and then reverse its movement to make the same travel until reaching the other surfacec
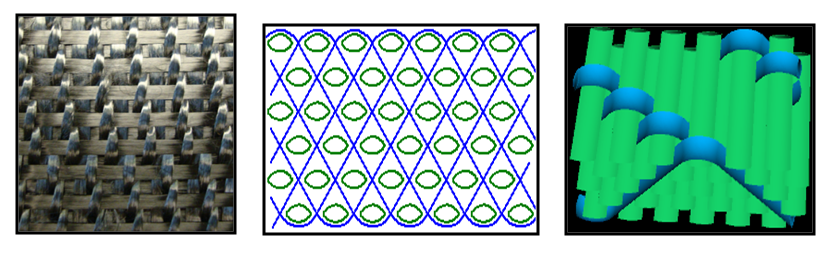
4. Angle Interlock Layer-to-Layer [Regular & Modified]
In layer-to-layer fabric, bias yarns travel between two successive fabric layers making interlacements with several filling yarns according to the weave pattern
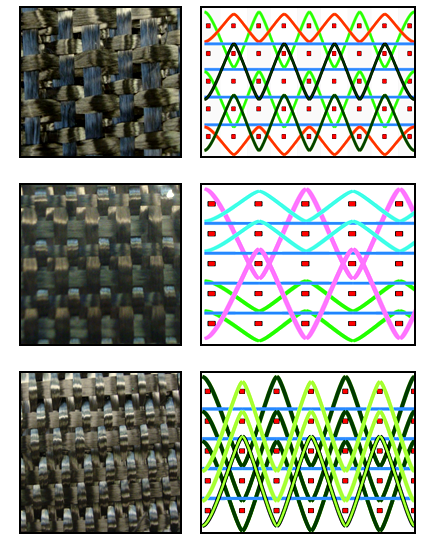
4. 3D Hollow Fabrics
- 3-D hollow woven preforms can be generally divided into two types, one with flat top and bottom surfaces and the other with uneven surfaces. Both can be manufactured based on the conventional weaving technology. The hollow fabrics can be made in a single level or multiple levels. The cross-sectional shape can be trapezoidal, triangular, or rectangular or honeycomb cell type.
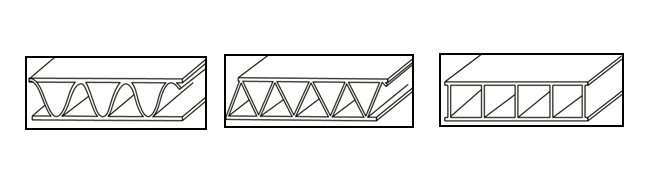
- 3D hollow fabrics with uneven surfaces are based on the multi-layer principle according to which the adjacent layers of fabrics are combined and separated at arranged intervals.
- The combining and separating of adjacent layers allow the entire fabric to be opened after weaving to become a 3-D structure with cellular-shaped cells in the cross-section.
- Because of the opening of the structures, the top and bottom surfaces of this type of hollow structure are not flat.
