2D Fabrics
2D Woven fabrics are by far the most commonly used textile system for composite material applications. The woven structure is characterized by the orthogonal interlacing of two sets of yarns, called warp and weft yarns. The warp yarns are aligned with the direction of the fabric leaving the weaving equipment, which is also called the warp direction. 2D woven fabric has two yarn sets as warp (0°) and filling (90°) and interlaced to each other to form the surface. Woven fabrics can be formed into composite materials with fiber volume fractions as high as 65%. It has basically plain, twill and satin weaves and derivatives which are produced by traditional weaving.
1) Plain weave Fabric [1/1]
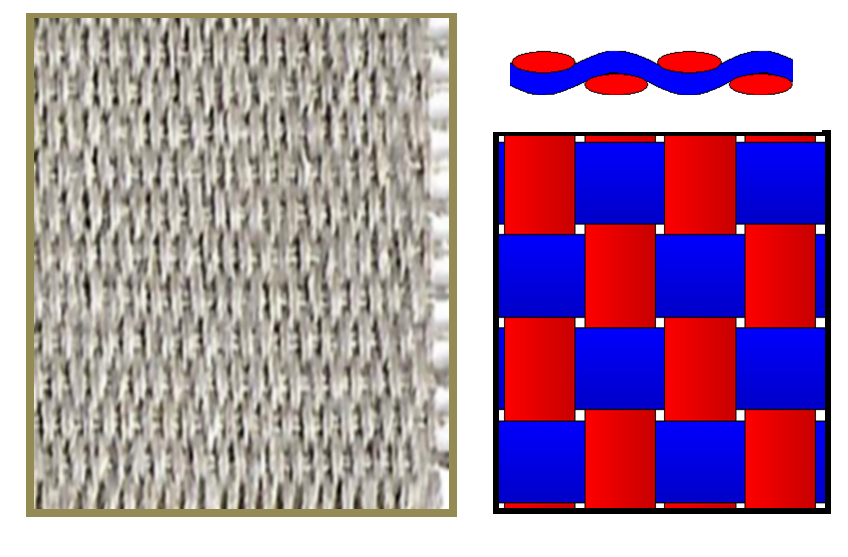
Plain weave is the most common and tightest of basic weave structures in which each warp fibre passes alternately under and over each weft fibre. The fabric is symmetrical, with good stability and reasonable porosity. However, it is the most difficult of the weaves to drape, and the high level of fibre crimp imparts relatively low mechanical properties compared with the other weave styles.
2)Twill [2/1, 3/1]
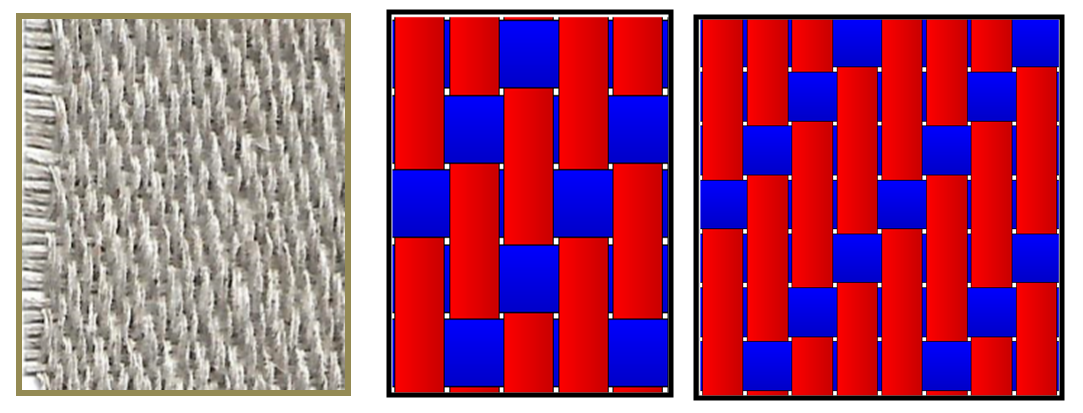
Twill is a type of textile weave with a pattern of diagonal parallel ribs. It can be identified by looking at the presence of pronounced diagonal lines that run along the width of the fabric. It has higher resistance to tearing than a plain weave because it has fewer yarns interlacing per area, therefore a greater degree of internal mobility. In addition, two yarns will bear the load when the fabric is torn
3) Sateen/Satin [5-end, 8-end]
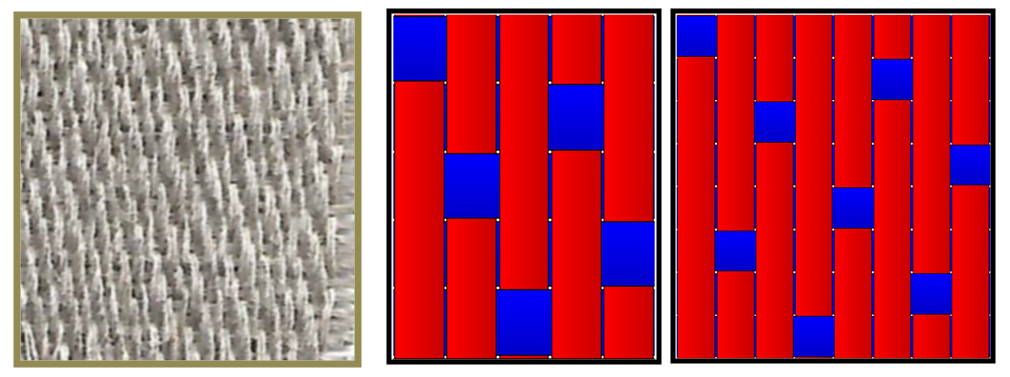
Satin is a weave that typically has a glossy surface and a dull back, one of three fundamental types of textile weaves along with plain weave and twill. The satin weave is characterized by four or more fill or weft yarns floating over a warp yarn, four warp yarns floating over a single weft yarn. Floats are missed interfacings, where the warp yarn lies on top of the weft in a warp-faced satin and where the weft yarn lies on top of the warp yarns in weft-faced satins.
4) Basket weave [2/2, 4/4]
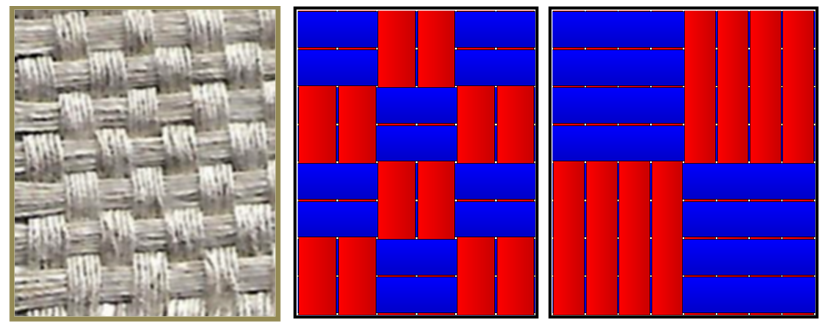
Basket weave is also known as Hopsack and Matt Weave. The Hopsack weave, a variation of the plain weave, uses two or more warp and/or two or more weft yarns side by side as one yarn. The hopsack weave is obtained by doubling or otherwise multiplying the interlacing points of the plain weave in both the warp and weft direction. These weaves are made with two or more weft yarns placed in the same shed. The interlacing pattern is similar to the plain weave, but two or more yarns follow the same parallel path. Matt designed fabrics are more flexible and wrinkle resistant because there are fewer interlacing per square inch. The fabrics look flatter than comparable regular plain weave fabrics. However, long floats snag easily. The matt designed cloth has a greater resistance to tearing. Matt design tends to give smooth surface fabrics. In the repeat size of the matt weave the numbers of warp and weft yarns are equal.
5) Rib weave [1/2, 2/2, 3/2]
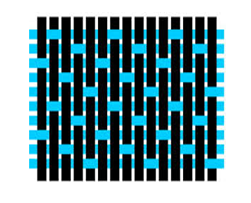
Rib weave is a variation of Plain weave and is created very similarly to a plain weave piece of fabric. The basic construction follows the same pattern of the weft yarns going under and over the warp yarns in the pattern of one under, one over and so on. The difference between plain weave and Rib weave is that Rib weave uses one heavyweight yarn. This is used for either the warp of weft yarns and the end result is a fabric that has raised ribs either horizontally or vertically down the fabric, depending on whether the heavier, thicker yarn is used for the warp or the weft.
6) Spread Tow Fabrics [Lightweight Specialty Woven Fabric]
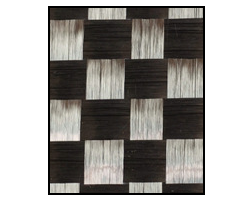
Spread tow refers to the practice of spreading a fiber into a thinner, flatter reinforcement, for example a 5-mm wide 12K high-strength (HS) carbon fiber tow is commonly spread to a 25-mm width tape. This unidirectional tape can then be used in automated tape laying (ATL) and automated fiber placement (AFP) processes. Spreading enables the tailoring of areal weight as well as other properties, such as resistance to crack propagation for improved damage tolerance. The flatness of spread tow means filaments are straighter than those bundled in normal fibers. This results in more efficient load-carrying capability, by weight, and improved surface finish, as well as an aesthetic appeal.