High Performance Structural Composites – An Insight
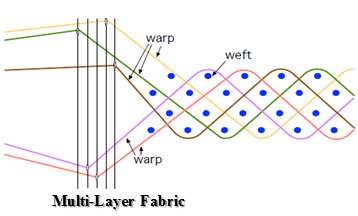
Introduction
Woven fabric reinforced composite materials manufactured using high performance fibre, offers the highest potential for the development of high performance structural components especially for aerospace and automotive, renewable energy and civil construction application. High performance structural composite materials utilizes 2D woven 3D shaped textile fabric structure designed by manipulating high performance fibres such as Carbon, Glass, Aramids and combination thereof, put together into a near-net shape essentially termed as “Preforms” as illustrated in figure 1. The design of textile composites requires a systematic approach that integrates micro-structural design, preform fabrication and composite processing to produce load-bearing structural components with desired mechanical properties. These 2D woven and 3D shaped textile preforms are developed on customly designed purpose built machines.
Pre-orientating the dry fibres into a desired 2D woven 3D near-net shape, with good reproducibility along with integration of the manufacturing process with inspection and quality assurance at minimum cost significantly reduces the cost of the finished component as illustrated in figure 2
Figure – 2: Production process of 2D woven 3D shaped components
Additionally the use of liquid composite moulding (LCM), techniques such as vacuum infusion (VI) and Resin Transfer Molding (RTM), in combination with near-net shaped dry textile fibre preforms can contribute significantly to post-treatment free composite manufacturing as shown in figure 3
Two Dimensionally Woven 3D Shaped Fabrics as Reinforcement
Two dimensionally woven 3D shaped woven textile structural composite materials carry specific features such as strength to stiffness to weight ratios which enable them to penetrate to the industries like, civil construction, biomedical, leisure and even art and design applications. These materials offer light yet strong drapeable and moldable textiles where reinforcement properties can be tailored to meet application requirements in specific areas within the single component. Their potential for cost-effective processing results reduction in waste makes them preferable in aerospace industry over other available materials.
Two dimensionally woven 3D shaped dry fibre preforms for reinforcing composites were manufactured with modified conventional two dimensional weaving equipment that facilitate the introduction of through-the-thickness yarns in a single process. Near-net-shape preforms can be rapidly manufactured using a variety of fibrous materials into complex shaped geometries tailored to specific applications including airfoils, fan blades, radomes, tubes, bifurcated shapes, contours and structural cross-sections such as T’s, Pi, and X’s. The shaped dry reinforcement is then processed into a three dimensional ceramic matrix composite for high-temperature components requiring thermal shock resistance, such as rocket motor nozzles. Regardless of the material, advances in the design software, computer-aided-design tools, and finite element analysis are fostering the production of complicated shapes and profiles that feature targeted fibre orientation and application-specific mechanical properties more accurately than in the past.
Three dimensionally woven fabrics when transformed into composites have exhibits excellent delamination resistance and high impact damage tolerance properties which are must for high end and performance demanding application.
Present Manufacturing Scenario in the World Composites Industry
The global composites market size is projected to grow from USD 74.0 billion in 2020 to USD 112.8 billion by 2025, at a CAGR of 8.8%. The major driver behind the growth of composite industry is the demand of light-weight materials from the aviation sectors especially, military applications such as airplanes, helicopters and rockets, targeting the important issues like reduction in fuel consumption, increased service life and the safety. Currently, the aviation industry utilizes 2D composite laminated materials made from Prepregs coupled with autoclave processing which is very slow and induces high cost which makes them less affordable though the composite material exhibits superior mechanical properties. The major issues with the use of Prepregs are their limited shelf life and require constant refrigeration for storage which incurs additional cost. In the past few decades, technologies such as stitched-RTM, filament winding, Pultrusion, automatic tape laying and automatic fibre placement etc, has been well developed. However, all these highly developed technologies have some noteworthy disadvantages in terms of material processing and handling of complex shaped geometries.
Stitched-RTM technique is well suited only for small and medium size component i.e. available equipment’s can only handle limited thickness dry preforms and have limitations toward component shape.
Filament winding processes which are been in use since a long time is still unable to manufacture components of variable thickness with consistent quality. It also suffers from rigidity with fibre orientation and inability to wind non axis-symmetric shapes such as ‘T’ and elbow shapes. The most critical problem identified with filament winding process is the control of fibre tension during fibre deployment on the mandrel surface.
The Pultrusion technology has considerable potential for reducing the cost of manufacturing but, the existing technology can only design parts with constant cross-sectional shapes. The process has a limitation towards fibre orientation and is also unable to pultrude complex multi-element cross-sections such as ‘J’- stiffened panels, hexagons, and constant airfoil sections. Another important disadvantage associated with this technology is its inability to vary the size of the tube to impart constant taper shape.
The automatic tape lay-up (ATL) technique has made significant progress in the past two decades in terms of speed and accuracy. This is mainly due to the advancements in computer technology which facilitates the writing of complex programs but, still there is a space for developing complex programs to suit the lay-up in complex contoured components.
Robotic dry tow placement is a relatively new process which has drawn considerable attention in recent years as it disseminates the advantages of both ATL and filament winding. It has a considerable potential to cut down the production costs however, but its capability for generating high production rates is still in question due to non-availability of optimized control systems, head position feedback and in-process inspection for fast, accurate and high quality parts production. All the existing techniques discussed above have a common disadvantage of not facilitating through-the-thickness reinforcement in the composites. One of the possible solutions to this problem is the application of highly developed tufting technique but, it only supports the ATL and robotic tow placement. However, the tufting process itself leads to fibre breakage which in turn results in reduction in mechanical performance of the resulting composite material.
Another promising and potential solution to address the problems with the above discussed technologies is the use of 3-D woven composites materials. These materials are dry fibre textiles distinguished by their orientation of yarn in three principle axis i.e. x, y and z directions. The fibres can be oriented in multiple directions in a single process, unlike 2-D laminates composite materials where, fibres are typically reinforced only in the plane of the laminate. Three dimensional woven composite materials can exhibit different material properties throughout a single component due to their tailor-ability and capability to form near-net shapes, which is the crucial advantage with this technology. Currently, the 3D weaving technology is in its basic state of development and has some important issues that need to be accurately addressed and essentially resolved to make the process cost-effective and flexible. High-performance composites have features like high durability, lightweight, and good heat resistivity which have been propelling the rise in demand for the same within aerospace, automotive, construction, energy, and medical industries. Reducing the curb weight of automotive and aircrafts results in the increase in efficiency and lowering fuel consumption boosting demand from the automotive & aerospace industry.